What are the necessary processes for PCBA proofing?
Key processes and key points of PCBA proofing
In the electronic equipment manufacturing industry, PCBA proofing is a crucial link. It is not only a preliminary verification of product research and development, but also the basis for ensuring the quality and stability of the final product.
Key processes and key points of PCBA proofing
1. Circuit board design and review
The first step of PCBA proofing is circuit board design. This is usually completed by electronic engineers using professional electronic design automation (EDA) tools. The design stage needs to consider multiple aspects such as circuit layout, component arrangement, signal integrity, and power distribution. After the design is completed, a strict review must be conducted to ensure the rationality and feasibility of the circuit design.
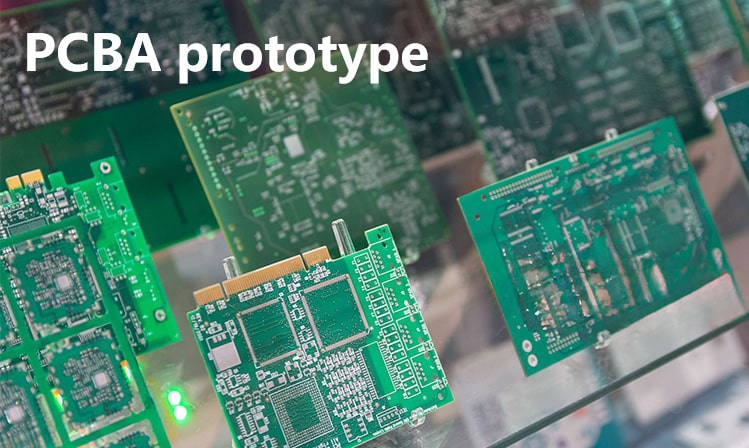
Key points of design review:
1. Whether the layout of the power supply and ground wires is reasonable: whether there is a potential risk of short circuit or open circuit.
2. Whether the spacing between components meets the production process requirements: to avoid problems such as bridging or cold soldering during the production process.
3. Whether the direction and length of the signal line are reasonable: to reduce signal interference and attenuation.
2. Material selection and procurement
After the design review is passed, the next step is to select and purchase the required materials. This includes circuit board substrates, electronic components, pads, connectors, etc. The choice of materials has a crucial impact on the stability and reliability of PCBA prototype.
Material selection points:
- Select materials from suppliers with high quality and good reputation.
- Electronic components should comply with relevant standards and specifications and have necessary certifications.
- For key components, strict screening and testing should be carried out to ensure their stable performance.
3. PCBA processing and weldingAfter the materials are ready, you can enter the PCBA processing and welding stage. This stage includes the production of circuit boards, the mounting of components, welding, and subsequent cleaning and testing.
Main points for processing and welding:
- When making circuit boards, ensure that the lines are clear and there are no short circuits or open circuits.
- The components should be mounted accurately to avoid position deviation or polarity errors.
- During the welding process, the welding temperature and time should be controlled to avoid damage to the components.
- The cleaning process should be thorough to remove the residues and dirt generated during the welding process.
4. Functional testing and verificationOne of the core links of PCBA proofing is functional testing and verification. This stage aims to ensure that the circuit board can operate stably under various working conditions and meet the design requirements.
Functional test and verification content:
- Power supply test: verify the stability and efficiency of the power supply circuit to ensure that the circuit board can work normally under different voltage and current conditions.
- Signal integrity test: evaluate the rationality of the circuit board design by testing the transmission quality and stability of the signal.
- Environmental adaptability test: including tests under environmental conditions such as high temperature, low temperature, humidity, etc. to verify the reliability and durability of the circuit board.
5. Problem location and modification
If problems are found during the test, problem location and modification are required. This stage is crucial to ensure the final quality of the circuit board.
Problem location and modification points:
- Use professional testing instruments and equipment to accurately find the problem.
- Carefully analyze the cause of the problem: it may be a design defect, component failure or welding problem, etc.
- Make corresponding modifications and optimizations to the problem, and then retest and verify.
6. Aging test and final verificationIn order to ensure the long-term stable operation of the circuit board, aging test is an indispensable link. By simulating various situations of the circuit board during long-term work, its stability and reliability can be tested.
Aging test content:
- Continuous work test: Let the circuit board work continuously for a period of time to observe its performance and stability.
- High and low temperature cycle test: By simulating extreme temperature conditions, the temperature resistance and stability of the circuit board can be tested.
- Vibration and shock test: Simulate the vibration and shock that the circuit board may encounter during transportation or use.
After the aging test is completed, final verification is required. This stage mainly conducts comprehensive functional and performance tests on the circuit board to ensure that it meets the design requirements and has stable performance.
The PCBA proofing process involves multiple key links, from design review to material selection, to processing and welding, functional testing and verification, problem location and modification, and aging testing and final verification. Each link is crucial and cannot be ignored. As a purchaser of an electronic equipment manufacturer, understanding and mastering these processes is of great significance to ensuring the stability and reliability of the circuit board.