PCBA reliability testing: the key to ensuring the durability of electronic products
In the field of electronic product manufacturing, the reliability of PCBA (printed circuit board assembly) directly determines the quality and life of the final product. Whether it is a smartphone, medical device or automotive electronic system, it needs to undergo rigorous reliability testing before it can be put on the market.
PCBA reliability testing
PCBA reliability testing is a series of testing methods that evaluate whether the circuit board assembly can work stably for a long time by simulating various environmental and operating conditions that the product may encounter in actual use. Just like athletes need to undergo various physical tests before the game, electronic products also need to pass these "physical examinations" to prove their "physical fitness".
Common PCBA reliability test items
1. Environmental adaptability test
Temperature cycle test: let the PCBA switch repeatedly between extremely cold and extremely hot environments to detect whether the expansion and contraction of the material will cause cracking or connection failure
High temperature and high humidity test: simulate humid and hot environment to test moisture resistance and insulation resistance
Salt spray test: for coastal or industrial environment, test corrosion resistance
2. Mechanical performance test
Vibration test: simulate vibration during transportation or use to check whether the solder joints are firm
Impact test: detect the product's ability to withstand sudden drops or collisions
Bending test: evaluate the reliability of the circuit board when it is deformed by force
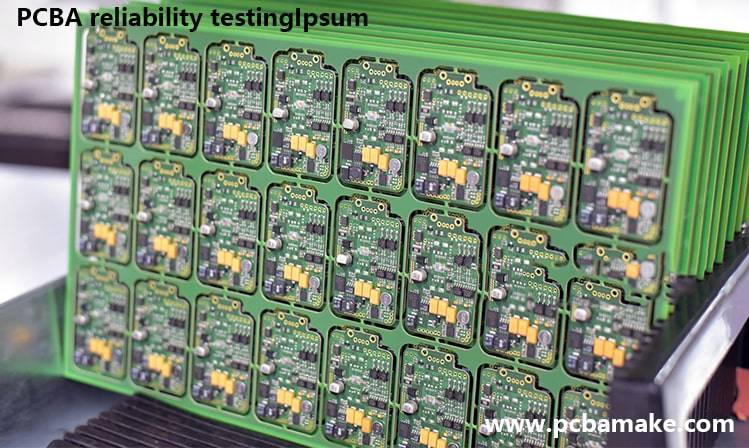
3. Electrical performance test
Power-on aging test: long-term power-on work to screen early faults
Insulation resistance test: ensure that there is no leakage between different circuits
Withstand voltage test: verify whether the insulating material can withstand high voltage without breakdown
4. Welding quality test
Solder joint strength test: measure the ability of solder joints to withstand tensile force
Microscopic section analysis: use a microscope to check whether the internal structure of the solder joint is intact
X-ray inspection: check internal welding defects that are invisible to the naked eye
Common test standards in the industry
Different industries have different "examination standards", the common ones are:
Consumer electronics: IPC-A-610, J-STD-001
Automotive electronics: AEC-Q100, ISO 16750
Military products: MIL-STD-810
Industrial equipment: IEC 60068 series
These standards are like textbooks for different subjects, stipulating the specific methods and qualification standards for testing.
Benefits of reliability testing
Improve product quality: discover potential defects in advance and avoid defective products from entering the market
Reduce after-sales costs: reduce the failure rate during product use and save repair and return costs
Enhance brand reputation: reliable products can win customer trust and reputation
Shorten time to market: product certification can be completed faster through standardized testing
Extend product life: ensure that the product works stably within the design life cycle
PCBA reliability testing is an indispensable part of the electronic product manufacturing process. It is like a "health checkup" for the product, helping manufacturers to discover problems and improve designs in advance. As the application environment of electronic products becomes increasingly complex, the standards and methods of reliability testing are also evolving. Choosing a PCBA manufacturer that attaches importance to reliability testing, such as PCBAMak, is an important insurance for the quality of your product.